What is optical mirror
Optical Mirrors are designed to reflect light for a variety of applications, including beam steering, interferometry, imaging, or illumination. Optical Mirrors are used in a wide range of industries, such as life sciences, astronomy, metrology, semiconductor, or solar.
Hyperion Optics offers a range of laser, flat, metal substrate, focusing, or specialty Optical Mirrors in a multitude of reflective coating options, including Protected Aluminum, Enhanced Aluminum, Protected Silver, Protected Gold, or Dielectric. Choosing the proper reflective coating option ensures high reflectivity of the needed wavelength or wavelength range. Optical Mirrors designed for laser applications are optimized for the given laser wavelength. Additionally, Optical Mirrors designed for lasers feature damage thresholds that are suitable for the designated laser. Metal substrate Optical Mirrors are ideal for applications requiring a constant coefficient of thermal expansion between the Optical Mirror and the mount. Optical Mirrors with a concave surface are ideal for light focusing applications.
Optical mirrors have a smooth, highly-polished, plane or curved surface for reflecting light. Usually, the reflecting surface is a thin coating of silver, or aluminum on glass. Product specifications for optical mirrors include diameter, radius of curvature, thickness focal length, and surface quality. The diameter or height of an optical mirror is measured straight on. If the optical mirror’s curvature was extrapolated into a sphere, then the radius of that sphere is the radius of curvature for the mirror. There are two thickness measurements for optical mirrors: center thickness and edge thickness. Units of measure include inches, feet, and yards; nanometers, centimeters, and millimeters, and miles and kilometers. With optical mirrors, focal length is the distance from the mirror at which light converges. Surface quality describes digs and scratches. A dig is a defect on a polished optical surface that is nearly equal in terms of length and width. A scratch is a defect whose length is many times its width.
Optical mirrors are made from many different materials, each of which influences the mirror’s reflectivity characteristics. Choices for materials include borosilicate glass, copper, fused silica, nickel, and optic crown glass. Borosilicate glass is also known as BK7 and boro-crown glass. Copper is used in high-power applications because of its high thermal conductivity. Fused silica has a very low coefficient of thermal expansion and is suitable for use with moderately-powered lasers or changing environmental conditions. Ultraviolet (UV) grade optical mirrors are also commonly available. Nickel is used in applications which require resistance to both thermal and physical damage. Proprietary materials for optical mirrors include Pyrex (Corning Inc.) and Zerodur (Schott Glaswerke).
Optical mirrors are sometimes coated to enhance their reflectivity. Choices include bare, enhanced, and protected aluminum; silver, bare gold and protected gold; and coatings made from rhodium and dielectric materials. Enhanced aluminum coatings are used to improve reflectance in the visible and ultraviolet regions. Protected aluminum coatings provide abrasion resistance while protecting the surface of the aluminum, an excellent reflector in the upper UV, visible and near-infrared (IR) regions. Optical mirrors with bare gold and protected gold coatings are used in the near-IR to far-IR regions. Silver coatings provide better reflectance than aluminum; however, silver’s tendency to oxidize and tarnish requires thorough sealing from the atmosphere. Rhodium coatings have a reflectivity of approximately 80% of the visible spectrum.
Heat mirrors and cold mirrors are special bandpass filters that can reflect infrared light and ultraviolet light and only allow visible light to pass through, also known as heat-absorbing filters, also known as IR cut filters. Heat Mirror will be a large number of heat generated near-infrared light isolated optical path to protect the heat-sensitive devices, where the need for high light intensity and need to be separated from the heat applications can be.
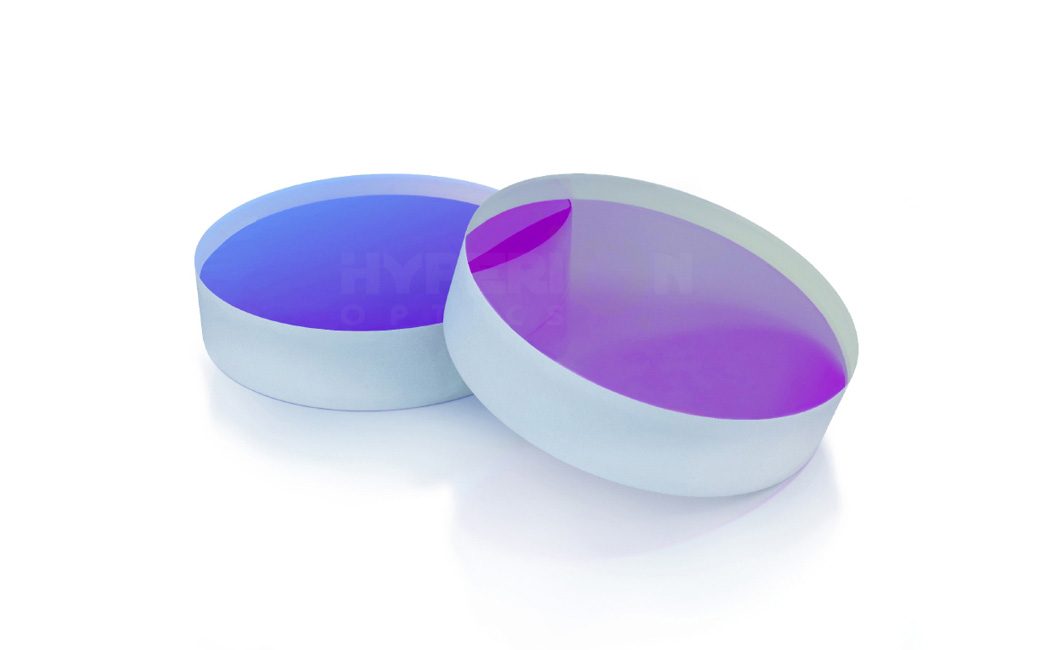
Reflective film from the coating material can generally be divided into two categories; one is the reflective metal film, one is all dielectric reflective film.
Media reflection film using the principle of multi-beam interference, which, contrary to the media anti-reflective film, can significantly improve the light in the air glass interface reflectivity. By alternately plating high and low refractive index multilayer films on the surface of the lens, the synthetic amplitude of the reflected light can be increased, and the reflectivity of the reflective film can be more than 99.9% of specially optimized design. In contrast, the reflectivity of the reflective metal film is only 97%.
Labels: Hyperion, mirror, optic china, optical mirror, optics
0 Comments:
Post a Comment
Subscribe to Post Comments [Atom]
<< Home